What is Porosity in Welding: Necessary Tips for Achieving Flawless Welds
The Scientific Research Behind Porosity: A Comprehensive Overview for Welders and Fabricators
Comprehending the elaborate systems behind porosity in welding is crucial for welders and makers making every effort for flawless workmanship. As metalworkers delve right into the depths of this sensation, they uncover a globe regulated by numerous aspects that affect the development of these small spaces within welds. From the make-up of the base products to the details of the welding procedure itself, a plethora of variables conspire to either intensify or minimize the existence of porosity. In this detailed overview, we will certainly unwind the science behind porosity, exploring its effects on weld top quality and introduction progressed strategies for its control. Join us on this trip through the microcosm of welding blemishes, where precision meets understanding in the quest of flawless welds.
Recognizing Porosity in Welding
FIRST SENTENCE:
Exam of porosity in welding exposes important insights right into the stability and high quality of the weld joint. Porosity, characterized by the presence of cavities or voids within the weld metal, is a common concern in welding processes. These voids, if not properly dealt with, can jeopardize the architectural stability and mechanical properties of the weld, bring about potential failures in the completed product.
To find and evaluate porosity, non-destructive testing techniques such as ultrasonic testing or X-ray examination are commonly utilized. These techniques enable the identification of internal issues without jeopardizing the honesty of the weld. By examining the dimension, shape, and circulation of porosity within a weld, welders can make enlightened choices to enhance their welding procedures and accomplish sounder weld joints.
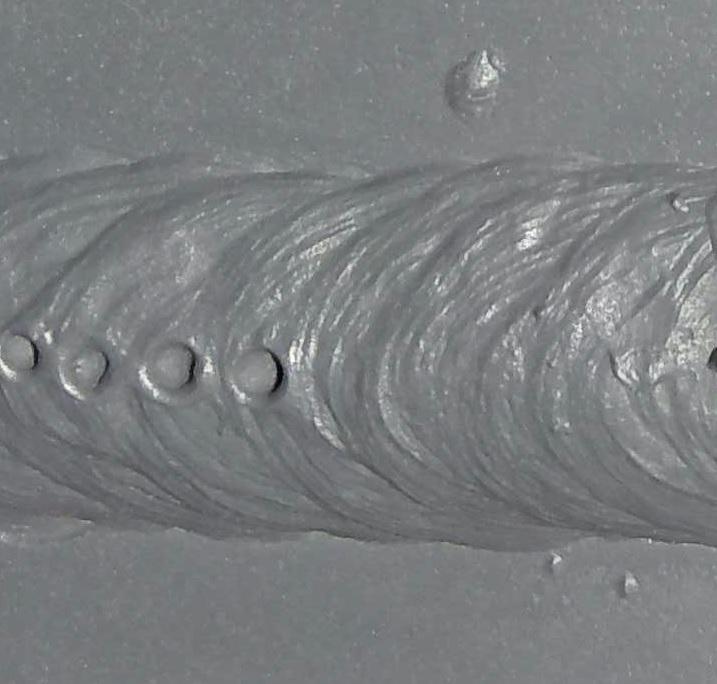
Elements Affecting Porosity Development
The event of porosity in welding is affected by a myriad of aspects, ranging from gas protecting effectiveness to the intricacies of welding specification settings. Welding criteria, including voltage, present, take a trip rate, and electrode kind, likewise effect porosity development. The welding technique employed, such as gas steel arc welding (GMAW) or shielded steel arc welding (SMAW), can influence porosity development due to variations in warm distribution and gas insurance coverage - What is Porosity.
Effects of Porosity on Weld Top Quality
The existence of porosity likewise damages the weld's resistance to rust, as the trapped air or gases within the spaces can respond with the surrounding environment, leading to deterioration over time. In addition, porosity can impede the weld's capacity to withstand stress or impact, further endangering the total high quality and dependability of the welded structure. In crucial applications such as aerospace, vehicle, or architectural building and constructions, where security and longevity are critical, the harmful impacts of porosity on weld quality can have serious consequences, emphasizing the relevance of lessening porosity via correct welding strategies and procedures.
Methods to Minimize Porosity
To improve investigate this site the top quality of welded joints and ensure architectural stability, welders and makers use certain strategies targeted at decreasing the development of gaps and dental caries within the product throughout the welding process. One efficient technique to minimize porosity is to make certain proper product prep work. This consists of thorough cleansing of the base metal to eliminate any impurities such as oil, oil, or moisture that might add to porosity formation. Furthermore, making use of the proper welding specifications, such as the correct voltage, existing, and take a trip rate, is important in protecting against porosity. Preserving a regular arc length and angle during welding additionally helps reduce the probability of porosity.

Moreover, selecting the appropriate protecting gas and preserving correct gas flow prices are necessary in decreasing porosity. Utilizing the appropriate welding strategy, such as back-stepping or employing a weaving movement, can likewise aid disperse warmth evenly and decrease the chances of porosity formation. Guaranteeing proper ventilation in the welding environment to eliminate any prospective sources of contamination is important for accomplishing porosity-free welds. By carrying out these methods, welders can efficiently lessen porosity and site web create high-quality bonded joints.
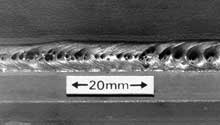
Advanced Solutions for Porosity Control
Applying sophisticated modern technologies and innovative approaches plays an essential duty in achieving superior control over porosity in welding procedures. In addition, employing sophisticated welding methods such as pulsed MIG welding or customized atmosphere welding can likewise aid minimize porosity issues.
Another advanced service entails the use of sophisticated welding tools. Using tools with integrated attributes like waveform control and sophisticated power sources can improve weld high quality and decrease porosity dangers. Furthermore, the application of automated welding systems with precise control over parameters can considerably decrease porosity defects.
Furthermore, incorporating sophisticated tracking and assessment modern technologies such as real-time X-ray imaging or automated ultrasonic testing can help in discovering porosity early in the welding process, permitting prompt corrective activities. In general, integrating these sophisticated options can significantly boost porosity control and boost the overall top quality of bonded elements.
Final Thought
In final thought, comprehending site here the science behind porosity in welding is necessary for welders and makers to generate top notch welds - What is Porosity. Advanced solutions for porosity control can further improve the welding procedure and ensure a solid and dependable weld.